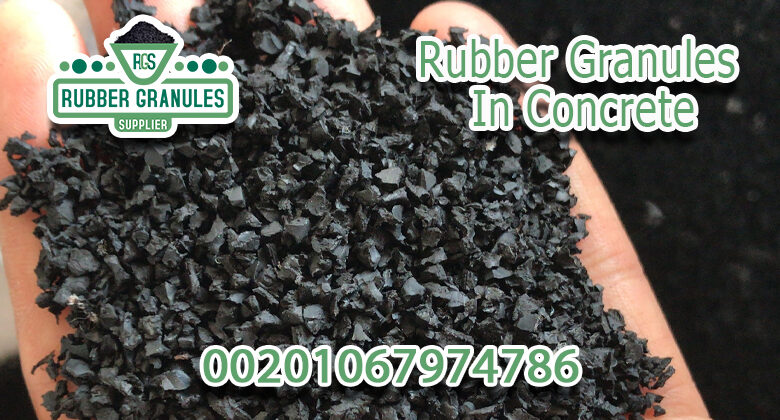
Rubber Granules in Concrete: Enhancing Sustainability and Performance 2025
Rubber Granules in Concrete: Enhancing Sustainability and Performance
In recent years, the incorporation of rubber granules in concrete has gained popularity as a sustainable and innovative solution in the construction industry. Incorporating rubber granules, typically made from recycled tires, into concrete creates a material that enhances durability and is also environmentally friendly.
The use of rubber granules offers a multitude of benefits, ranging from improved impact resistance to enhanced insulation properties. By replacing a portion of traditional aggregates with rubber granules, the resulting material becomes more flexible and less prone to cracking or spalling.

Rubber Granules In Concrete
Rubber Granules In Concrete
Concrete is a versatile material that is commonly used in construction due to its durability and strength. However, traditional concrete has limitations when it comes to impact flexibility. In recent years, researchers and construction professionals have been exploring the use of rubber granules to enhance its properties.
Rubber granules, made from tires, are being incorporated into asphalt mixtures to create a more flexible material. This innovative approach not only addresses the issue of waste tires but also improves the performance of concrete in different applications.
The addition of rubber granules can result in a material that is more elastic. This makes it ideal for areas prone to heavy foot traffic, such as playgrounds. In addition, rubberized concrete can also provide better insulation properties compared to traditional concrete.
As sustainability becomes a growing concern in the construction industry, the use of rubber granules offers a promising solution to reduce waste. This article will explore the benefits of using rubber granules and discuss the potential applications of this material.
How To Use Rubber Granules In Concrete
One way to incorporate rubber granules into concrete is by mixing the granules into the wet concrete mixture before pouring.
Another method is to sprinkle the rubber granules onto the surface of freshly poured concrete before it completely sets. This technique enables a more customized and textured finish by spreading the granules out in a pattern. It is important to note that we must carefully calculate the proportion of rubber granules to concrete to ensure the desired properties.
Too few granules may not provide enough impact resistance, while too many could compromise the structural integrity of the concrete
Rubber Cost
The cost of incorporating rubber granules into concrete can vary based on several factors. Firstly, the quantity of rubber granules required achieving the desired level of flexibility.
Furthermore, when calculating the total expense of using rubber granules, one should take labor costs into consideration. This includes the cost of mixing and incorporating the granules into the concrete mixture.
It is vital to weigh the benefits of incorporating rubber granules against the potential costs. While it may initially be more expensive than traditional concrete mixes, the long-term durability, flexibility, and reduced maintenance costs of rubberized concrete may prove to be a cost-effective investment in the overall longevity of the structure.
The Benefits of Rubber Granules in Concrete
Enhanced Durability and Flexibility
Traditional concrete, while known for its strength, often lacks flexibility, making it prone to cracking under stress or impact. By incorporating rubber granules, concrete gains improved impact resistance and elasticity. This enhancement makes rubberized concrete ideal for high-traffic areas such as playgrounds, parking lots, and sports facilities.
Environmental Benefits
The construction industry generates significant waste, and finding ways to repurpose materials is crucial for sustainability. Rubber granules are made from recycled tires, addressing the issue of tire waste. Using these granules in concrete helps reduce landfill waste and the demand for virgin materials, aligning with global sustainability goals.
Improved Insulation Properties
Rubberized concrete offers better insulation properties compared to traditional concrete. This can lead to energy savings in buildings, as the enhanced thermal performance helps maintain indoor temperatures more effectively, reducing the need for heating and cooling.
Rubber Granules in Concrete
The Composition of Rubberized Concrete
Rubber granules are typically mixed into the wet concrete mixture before pouring. This method ensures an even distribution of granules throughout the concrete, enhancing its properties uniformly. The proportion of rubber granules to concrete must be carefully calculated to achieve the desired balance of flexibility and structural integrity.
Surface Application Technique
Another method for incorporating rubber granules is to sprinkle them onto the surface of freshly poured concrete before it sets completely. This technique allows for customized, textured finishes, making it suitable for decorative applications such as patios, walkways, and garden paths.
Practical Applications

Rubber Granules In Concrete
Playgrounds and Recreational Areas
Rubberized concrete is particularly beneficial for playgrounds and recreational areas.
The enhanced impact resistance and flexibility reduce the risk of injuries from falls, providing a safer environment for children and athletes.
Sports Facilities
In sports facilities, rubberized concrete can be used for flooring in gymnasiums, tennis courts, and multipurpose sports courts. The improved elasticity and durability ensure a longer lifespan and better performance under high-impact activities.
Parking Lots and Driveways
The use of rubber granules in concrete for parking lots and driveways can lead to surfaces that are less prone to cracking and spalling. The enhanced flexibility accommodates temperature fluctuations and heavy vehicle loads, extending the life of the pavement.
How to Use Rubber Granules in Concrete
Mixing Process
Incorporating rubber granules into the concrete mixture involves adding the granules to the wet mix before pouring. The mixture must be thoroughly blended to ensure an even distribution of granules, which contributes to the overall performance of the concrete.
Surface Finishing
For surface applications, rubber granules can be sprinkled onto freshly poured concrete and then worked into the surface. This method allows for decorative and functional finishes, providing a non-slip surface that is both visually appealing and practical.
Rubber Granules Prices
Factors Affecting Rubber Granules Prices
The cost of rubber granules varies based on several factors:
- Source and Quality: Recycled rubber from high-quality tires tends to be more expensive due to better performance characteristics.
- Granule Size: Different sizes of granules are used for various applications, influencing the price. Finer granules might cost more due to additional processing.
- Quantity: Bulk purchases often lead to discounts, reducing the per-unit cost.
- Processing Techniques: The method used to produce the rubber granules, such as cryogenic or ambient grinding, affects the price. Cryogenic grinding, which involves freezing and shattering the rubber, is typically more costly.
Average Prices
On average, rubber granules can range from $220 to $240 per ton, depending on the factors mentioned above.
However, prices can vary significantly based on regional availability and market demand.

rubber granules in concrete
FAQs
Q: What are rubber granules made from?
A: Rubber granules are typically made from recycled tires, which helps address tire waste and promotes environmental sustainability.
Q: How do rubber granules enhance concrete?
A: Rubber granules improve the flexibility, impact resistance, and insulation properties of concrete, making it more durable and environmentally friendly.
Q: Can rubberized concrete be used in high-traffic areas?
A: Yes, rubberized concrete is ideal for high-traffic areas such as playgrounds, sports facilities, and parking lots due to its enhanced durability and flexibility.
Q: Is rubberized concrete more expensive than traditional concrete?
A: The initial cost may be higher, but the long-term benefits such as reduced maintenance and improved performance can make it a cost-effective investment.
Q: How are rubber granules incorporated into concrete?
A: Rubber granules can be mixed into the wet concrete mixture before pouring or sprinkled onto the surface of freshly poured concrete for a textured finish.
Q: What are the environmental benefits of using rubber granules in concretes?
A: Using rubber granules in concrete helps reduce landfill waste, repurpose recycled tires, and decrease the demand for virgin materials, contributing to sustainability.
Conclusion
The use of rubber granules in concrete offers a promising approach to enhancing sustainability and improving certain performance characteristics of concrete. While challenges remain, ongoing research and development efforts are focused on optimizing mix designs, improving bonding, and addressing durability concerns. As the demand for sustainable construction materials continues to grow, rubberized concrete is likely to play an increasingly important role in the future of concrete construction. Careful consideration of the challenges and implementation of appropriate mitigation strategies are essential for realizing the full potential of this innovative material.
Incorporating rubber granules into concrete is a revolutionary approach that addresses both performance and environmental concerns.
By enhancing the durability, flexibility, and insulation properties of concrete, rubber granules offer a sustainable solution for various construction applications.
As the industry continues to prioritize sustainability, the use of rubberized concrete is set to become increasingly prevalent, paving the way for a greener and more resilient future.
Finally,
Contact Us Today
- Website: www.rubbergranules-supplier.com
- Email: info@[email protected]
- WhatsApp: 00201067974786
- Facebook: rubber rolls